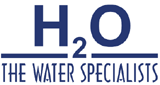
Project Involved
Partners
- Empex Toys
- Myrtha Pools
-
Goverment of Maharashtra Regulation8
On 14th Feb. 2002, Water Supply & Sanitation Department of Government of Maharashtra has issued a G.R approving Rain Water Harvesting as a means of improving water supplies. The G.R. details various techniques of Rain Water Harvesting, their costing & availability of funds. In furtherance Municipal Corporation of Greater Mumbai has issued a Circular insisting provisions for of Rain Water Harvesting while developing plots having area more than 1000 Sq.Mts, as I.O.D. conditions from 1st Oct. 2002. The design of Rain Water Harvesting system shall be prepared by approved consultant in the field & shall be to the satisfaction of the Corporation. Further all Centrally Air conditioned building shall have their own waste water treatment plant & treated waste shall be used for cooling purposes.
- SWIMMING POOLS / FOUNTIANS
As Consultant for amusement park, resort, water bodies and Swimming pools Guiding the client on the concept, design , drawings, execution and operations of the park. - WATER PARK
A Water Park is an amusement park that features water play areas - INDOOR / NATOTORIUM WATER PARK
A Water Park is an amusement park that features water play areas - OUTDOOR WATER PARK
A Water Park is an amusement park that features water play areas - THEME AND AMUSEMENT PARKS
Amusement park and theme park are terms for a group of entertainment attractions and rides - FUNHOUSE
is a facilityin which animals are confined within enclosures, displayed to thepublic, and in which they may also be bred - WATER SPA
Water Spa is expert job and should be carried by one.
Rain water harvest
This is a free Service to anyone seeking to do rain water harvesting for non profit basis
A rainwater harvesting system comprises components of various stages - transporting rainwater through pipes or drains, filtration, and storage in tanks for reuse or recharge. The common components of a rainwater harvesting system involved in these stages are illustrated here.
1. Catchments: The catchment of a water harvesting system is the surface which directly receives the rainfall and provides water to the system. It can be a paved area like a terrace or courtyard of a building, or an unpaved area like a lawn or open ground. A roof made of reinforced cement concrete (RCC), galvanised iron or corrugated sheets can also be used for water harvesting.
2. Coarse mesh at the roof to prevent the passage of debris
3.Gutters: Channels all around the edge of a sloping roof to collect and transport rainwater to the storage tank. Gutters can be semi-circular or rectangular and could be made used
Locally available material such as plain galvanised iron sheet (20 to 22 gauge), folded to required shapes.
Semi-circular gutters of PVC material can be readily prepared by cutting those pipes into two equal semi-circular channels.
Bamboo or betel trunks cut vertically in half.
The size of the gutter should be according to the flow during the highest intensity rain. It is advisable to make them 10 to 15 per cent oversize.
Gutters need to be supported so they do not sag or fall off when loaded with water. The way in which gutters are fixed depends on the construction of the house; it is possible to fix iron or timber brackets into the walls, but for houses having wider eaves, some method of attachment to the rafters is necessary.
4.Conduits: Conduits are pipelines or drains that carry rainwater from the catchment or rooftop area to the harvesting system. Conduits can be of any material like polyvinyl chloride (PVC) or galvanized iron (GI), materials that are commonly available.
The following table gives an idea about the diameter of pipe required for draining out rainwater based on rainfall intensity and roof area:
Sizing of rainwater pipe for roof drainage
Diameter Of pipe (mm) |
Average rate of rainfall in mm/h |
|||||
50 |
75 |
100 |
125 |
150 |
200 |
|
50 |
13.4 |
8.9 |
6.6 |
5.3 |
4.4 |
3.3 |
65 |
24.1 |
16.0 |
12.0 |
9.6 |
8.0 |
6.0 |
75 |
40.8 |
27.0 |
20.4 |
16.3 |
13.6 |
10.2 |
100 |
85.4 |
57.0 |
42.7 |
34.2 |
28.5 |
21.3 |
125 |
- |
- |
80.5 |
64.3 |
53.5 |
40.0 |
150 |
- |
- |
- |
- |
83.6 |
62.7 |
5. First-flushing: A first flush device is a valve that ensures that runoff from the first spell of rain is flushed out and does not enter the system. This needs to be done since the first spell of rain carries a relatively larger amount of pollutants from the air and catchment surface.
6. Filter: The filter is used to remove suspended pollutants from rainwater collected over roof. A filter unit is a chamber filled with filtering media such as fibre, coarse sand and gravel layers to remove debris and dirt from water before it enters the storage tank or recharge structure. Charcoal can be added for additional filtration.(i) Charcoal water filter A simple charcoal filter can be made in a drum or an earthen pot. The filter is made of gravel, sand and charcoal, all of which are easily available.
(ii) Sand filters Sand filters have commonly available sand as filter media. Sand filters are easy and inexpensive to construct. These filters can be employed for treatment of water to effectively remove turbidity (suspended particles like silt and clay), colour and microorganisms.
In a simple sand filter that can be constructed domestically, the top layer comprises coarse sand followed by a 5-10 mm layer of gravel followed by another 5-25 cm layer of gravel and boulders.
(ii. a) Dewas filters Most residents in Dewas, Madhya Pradesh, have wells in their houses. Formerly, all that those wells would do was extract groundwater. But then, the district administration of Dewas initiated a groundwater recharge scheme. The rooftop water was collected and allowed to pass through a filter system called the Dewas fillter, designed by Mohan Rao , district collecter of Dewas, and engineers of the rural engineering services. The water thus filtered is put into the service tubewell. The filter consists of a polyvinyl chloride (PVC) pipe 140 mm in diameter and 1.2m long. There are three chambers. The first purification chamber has pebbles varying between 2-6 mm, the second chamber has slightly larger pebbles, between 6 and 12 mm and the third chamber has the largest - 12-20 mm pebbles. There is a mesh at the outflow side through which clean water flows out after passing through the three chambers. The cost of this filter unit is Rs 600.
Filter for large rooftops When rainwater is harvested in a large rooftop area, the filtering system should accommodate the excess flow. A system is designed with three concentric circular chambers in which the outer chamber is filled with sand, the middle one with coarse aggregate and the inner-most layer with pebbles.
7. Storage facility: There are various options available for the construction of these tanks with respect to the shape, size and the material of construction.



8. Recharge structures: Rainwater may be charged into the groundwater aquifers through any suitable structures like dugwells, borewells, recharge trenches and recharge pits.
Various recharge structures are possible - some which promote the percolation of water through soil strata at shallower depth (e.g., recharge trenches, permeable pavements) whereas others conduct water to greater depths from where it joins the groundwater (e.g. recharge wells). At many locations, existing structures like wells, pits and tanks can be modified as recharge structures, eliminating the need to construct any structures afresh. Here are a few commonly used recharging methods:
1. Recharging of dugwells and abandoned tubewells.
In alluvial and hard rock areas, there are thousands of wells which have either gone dry or whose water levels have declined considerably. These can be recharged directly with rooftop run-off. Rainwater that is collected on the rooftop of the building is diverted by drainpipes to a settlement or filtration tank, from which it flows into the recharge well (borewell or dugwell).
If a tubewell is used for recharging, then the casing (outer pipe) should preferably be a slotted or perforated pipe so that more surface area is available for the water to percolate. Developing a borewell would increase its recharging capacity (developing is the process where water or air is forced into the well under pressure to loosen the soil strata surrounding the bore to make it more permeable).
If a dugwell is used for recharge, the well lining should have openings (weep-holes) at regular intervals to allow seepage of water through the sides. Dugwells should be covered to prevent mosquito breeding and entry of leaves and debris. The bottom of recharge wells should be desilted annually to maintain the intake capacity
Providing the following elements in the system can ensure the quality of water entering the recharge wells:
1. Filter mesh at entrance point of rooftop drains
2. Settlement chamber
3. Filter bed
A settlement chamber
2. Settlement tank
Settlement tanks are used to remove silt and other floating impurities from rainwater. A settlement tank is like an ordinary storage container having provisions for inflow (bringing water from the catchment), outflow (carrying water to the recharge well) and overflow. A settlement tank can have an unpaved bottom surface to allow standing water to percolate into the soil.
In case of excess rainfall, the rate of recharge, especially of borewells, may not match the rate of rainfall. In such situations, the desilting chamber holds the excess amount of water till it is soaked up by the recharge structure. Thus, the settlement chamber acts like a buffer in the system.
Any container, (masonry or concrete underground tanks, old unused tanks, pre-fabricated PVC or ferrocement tanks) with adequate capacity of storage can be used as a settlement tank.
3. Recharging of service tubewells.
In this case the rooftop runoff is not directly led into the service tubewells, to avoid chances of contamination of groundwater. Instead rainwater is collected in a recharge well, which is a temporary storage tank (located near the service tubewell), with a borehole, which is shallower than the water table. This borehole has to be provided with a casing pipe to prevent the caving in of soil, if the strata is loose. A filter chamber comprising of sand, gravel and boulders is provided to arrest the impurities.
4. Recharge pits
A recharge pit is 1.5m to 3m wide and 2m to 3m deep. The excavated pit is lined with a brick/stone wall with openings (weep-holes) at regular intervals. The top area of the pit can be covered with a perforated cover. Design procedure is the same as that of a settlement tank.
5. Soakaways / Percolation pit
Filter materials in a soakaway
Percolation pits, one of the easiest and most effective means of harvesting rainwater, are generally not more than 60 x 60 x 60 cm pits, (designed on the basis of expected runoff as described for settlement tanks), filled with pebbles or brick jelly and river sand, covered with perforated concrete slabs wherever necessary.
6.Recharge trenches
A recharge trench is a continuous trench excavated in the ground and refilled with porous media like pebbles, boulders or broken bricks. A recharge trench can be 0.5 m to 1 m wide and 1 m to 1.5 m deep. The length of the recharge trench is decided as per the amount of runoff expected. The recharge trench should be periodically cleaned of accumulated debris to maintain the intake capacity. In terms of recharge rates, recharge trenches are relatively less effective since the soil strata at depth of about 1.5 metres is generally less permeable. For recharging through recharge trenches, fewer precautions have to be taken to maintain the quality of the rainfall runoff. Runoff from both paved and unpaved catchments can be tapped.
7.Recharge troughs
To collect the runoff from paved or unpaved areas draining out of a compound, recharge troughs are commonly placed at the entrance of a residential/institutional complex.These structures are similar to recharge trenches except for the fact that the excavated portion is not filled with filter materials. In order to facilitate speedy recharge, boreholes are drilled at regular intervals in this trench. In design part, there is no need of incorporating the influence of filter materials.
This structure is capable of harvesting only a limited amount of runoff because of the limitation with regard to size.
8. Modified injection well
In this method water is not pumped into the aquifer but allowed to percolate through a filter bed, which comprises sand and gravel. A modified injection well is generally a borehole, 500 mm diameter, which is drilled to the desired depth depending upon the geological conditions, preferably 2 to 3 m below the water table in the area. Inside this hole a slotted casing pipe of 200 mm diameter is inserted. The annular space between the borehole and the pipe is filled with gravel and developed with a compressor till it gives clear water. To stop the suspended solids from entering the recharge tubewell, a filter mechanism is provided at the top.
Construction
Procedures and specifications for construction of storage and recharge tanks are explained below. There are a lot of similarities in the construction steps of both storage and recharge structures.
Construction of a masonry tank under progress
I. Masonry Tanks: When building brick walls for water tanks, both horizontal and vertical joints are filled with mortar of a ration of 1:4. For obtaining maximum strength, lay out a circle of bricks or blocks on the foundation without mortar, with such spacing that no brick or block is cut to fit into the circle. A proper foundation of cement concrete will also have to be provided.




I. part cement to 10 parts lime.
II. Reinforced Cement Concrete Tank (RCC) Reinforced concrete tanks can be built above or below the ground. Concrete is durable and long-lasting, but is subject to cracking. An advantage of concrete cisterns is their ability to decrease the corrosiveness of rainwater by allowing the dissolution of calcium carbonate from the walls and floors. Each tank must have an overflow system for situations when excess water enters the tank. The overflow can be connected to the drainage system. Design and construction of reinforced cement concrete tanks shall comply with the requirements of IS 3370 (part-I)-1965 and IS 456-1964. Accordingly the mix of cement concrete shall not be leaner than 1:2:4 ( 1 part cement: 2 parts of coarse sand and 4 parts of stone aggregates of 20 mm nominal size) When constructing water tanks it is essential to adhere to a few basic yet critical rules with respect to correct mixtures and applications of concrete and mortar. These include:



III. Ferro Cement Jars: Ferrocement consists of a thin sheet of cement mortar which is reinforced with a cage made of wire mesh and steel bars. Because ferrocement is structurally more effectient than masonry, the thickness of the walls of the container are as low as 10 to 15 mm. Ferrocement components can be casted in any shape using suitable moulds. The technology is extremely simple to implement, and even semi-skilled workpersons can learn it with ease. Ferrocement requires only a few easily available materials - cement, sand, galvanized iron (GI) wire mesh, and mild steel (MS) bars - in small amounts compared to masonry and RCC.